Mid-sized rotary screw compressors from 25 to 125 hp
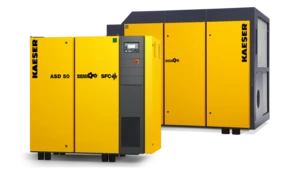
For us, a compressed air supply using rotary screw compressors represents the centerpiece of your production process. Our ASD, BSD, and CSD series ensure a dependable compressed air supply for your processes with unprecedented levels of efficiency.
These systems are perfect team players that can be integrated into existing control systems via the SIGMA AIR MANAGER 4.0. To ensure that you achieve the exact compressed air supply you require, our rotary screw compressors are available in different variants:
- Base model
- with refrigeration dryer for high compressed air quality: T model
- with variable-speed drive for optimum efficiency and a broad control range: SFC model
- with synchronous reluctance motor: Significantly greater efficiency – especially in the partial load range – than comparable asynchronous systems enables considerable energy savings.
- Complete systems with integrated refrigerated dryer and variable-speed drive: T SFC models
Our experts will be glad to assist you in selecting the right model for your needs.